Our Drug Product teams possess extensive experience in screening, optimizing, and scaling-up formulation and manufacturing processes for oral dosage forms and dry powder inhalers (DPI).
We excel in developing dosage forms whatever your API physical chemical characteristics and whatever the patient population you target, thanks to the wide panel of formulation technologies available (standard vs bioenhanced). Our scientists collaborate closely with partners to design and implement the most effective development strategy, ensuring a rapid and efficient entry into crucial First-in-Human studies. Furthermore, we advance the development of drug products for clinical supplies in Phase II and Phase III studies, developing robust formulations suitable for potential commercial purposes.
A Full Suite of Integrated DP Capabilities Combined With Expertise & Quality
Our experts understand your development needs and offer fast, high quality and efficient solutions tailored to your expectations and through all the drug product development phases.
Learn More
- Webinar Series: Mastering Quality By Design >
- Quality Risk Management >
- DoE Approach Applied to (TSWG) Platform: A Case Study >
- Rescuing the Unsolvable – A Case Study >

Formulation Screening
A comprehensive physicochemical properties assessment and the biopharmaceutical evaluation of your compound are the essential part of the initial formulation screening that starts in our labs. The close collaboration of interdisciplinary teams (Formulation, Analytical Development, Material Sciences, and Biopharmaceutics) as collective expertise enables to identify the most suitable formulation that aligns with your molecule's unique properties. This multidisciplinary approach significantly increases the success rate and shortens the duration of the screening phase, particularly for compounds which require bioavailability enhancement. The application of meticulous data analysis allows to select lead formulations for testing, providing results that meet the target criteria and using limited amounts of API.
Learn more about E.SOLVE: A formulation screening partner you can trust
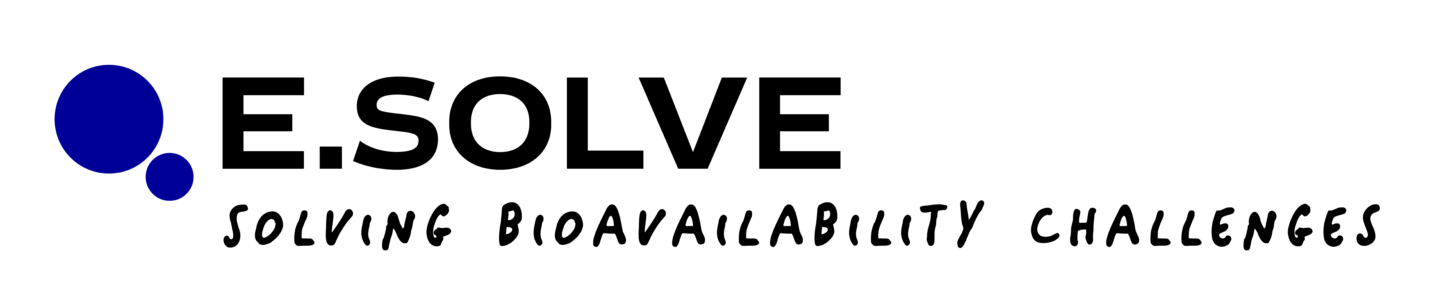
Small number of prototypes are prepared to evaluate the formulation performance and short-term physicochemical stability according to the agreed Target Product Profile.
ASAP Approach
The application of our Accelerated Stability Assessment Program (ASAP) approach allows us to reduce the duration while at the same time increasing the amount of information available for stability studies. View our Analytical Development and Quality Control capabilities to learn more about ASAP.
In Vitro and In Vivo Testing – All Under the Same Roof
Wide range of in vitro testing methods are applied, with specific expertise in developing discriminatory dissolution methods in bio-relevant media.
The co-location of the Animal Science Team allows quick in vivo testing in animals by the straightforward selection of the most relevant target animal species and study design, depending on the drug product properties to evaluate.
Rapid Drug Product Transfer to GMP Manufacturing
Our proven technology transfer process facilitates the transition of the selected formulation from non-GMP to the GMP facilities. The production of at least one batch of technical trial (demo) material confirms the suitability of the manufacturing process by utilizing representative or equivalent equipment throughout the formulation development stages.
Seamless Clinical Phases with Evotec's CMC Dossier-Ready Solutions
Evotec stands at the forefront of formulation development and process scale-up, with a proven track record as a pioneer in these fields. Our expertise extends to the implementation of the internationally recognized ICH Q8 and ICH Q9 guidelines, as well as the FDA's 2011 guidance and EMA annex 15 for process validation activities. By adhering to these principles, we enable seamless and continuous development throughout all clinical phases.
We emphasize the importance of accurate data collection and documentation, ensuring compliance with the highest standards required for Chemistry, Manufacturing, and Controls (CMC) dossiers.
Quality by Design
Quality by Design (QbD) is driven by a task force of qualified scientists who bring their expertise to design and implement comprehensive plans for development, registration, and process performance qualification. Supported by a team of expert statisticians, we employ powerful Design of Experiments (DoE) to design and interpret outcomes. Furthermore, we specialize in facilitating seamless technology transfer of externally developed formulations and processes to our manufacturing facility.
Clinical & Commercial Manufacturing
Our clinical supply capabilities cover a broad range of dosage forms for oral and inhalation delivery, with the possibility to handle highly potent compounds up to OEB5 (OEL>0.5 µg/m3) at various scales.
The perfect combination of flexibility and equipment scale supports small scale commercial manufacturing for niche therapeutic indications such as those required for rare diseases and orphan drugs.
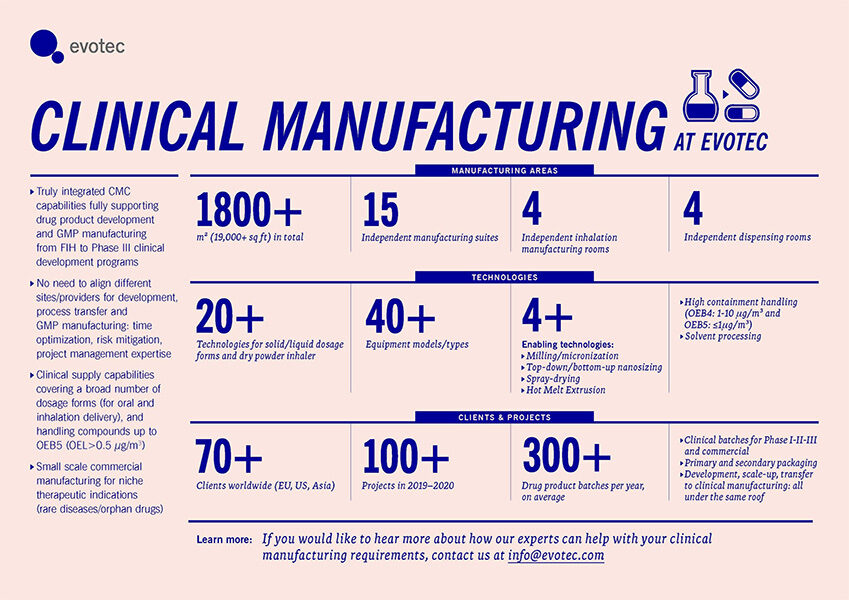
Our Special Capabilities
Quick in Humans
- Precise gravimetric filling of hard caspules with challenging powders (API alone or formulated) using Xcelodose™ and R1000 equipment
- Precise volumetric filling of small amounts of powders in hard capsules: FlexaLAB
- Gravimetric filling of powder (API alone or formulated) in bottles
Bioavailability Enhancement
- Micronization
- Nanosizing: top-down and bottom-up technologies
- Solid phase modification: amorphous solid dispersion via spray drying and hot melt extrusion, solid solution
- Lipid-based self-emulsifying systems
Dry Powder for Inhalation
- API characterization
- Particle engineering to modify particle morphology and enhance inhalation performances
- Precise filling technologies
- Reverse engineering of innovator DPI products
Patient Centric Approaches
- Multiparticulate: granules, pellets, powder for reconstitution
- Sprinkable capsules
- Nasogastric delivery
- Orally dispersable tablets
- Taste masking: by coating, by sweetening/flavoring
Modified Release
- Multiparticulate systems: coated pellets
- Enteric or controlled release coated tablets
- Controlled release matrix tablets
- PBPK gastroplus modeling
Our Manufacturing Technologies*
- Dry granulation
- High shear and fluid bed wet granulation
- Hot melt granulation
- Hot melt extrusion
- Pellet layering
- Micronization
- Wet bead milling (nanomilling)
- Antisolvent nanoprecipitation: clinical manufacturing (for oral application)
- Spray drying
- Liquid hard capsules filling and banding solutions
- Powder capsule filling
- Compression
- Tablet film coating
- Multiparticulate coating
*Small scale non-GMP to large-scale clinical manufacturing
Learn More
- Contact Our E.SOLVE Team >
- Clinical Manufacturing Infographic >
- Formulating Your Way to Successful Toxicology Studies Factsheet >
- E.SOLVE Factsheet >
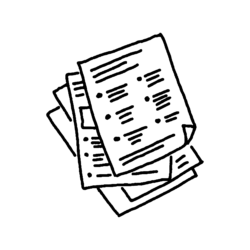