Just - Evotec Biologics produces biopharmaceutical drug substance for its clients to support clinical trials and commercial manufacturing with its continuous manufacturing platform. Our experts are experienced in the conversion of existing fed-batch processes to our platform irrespective of the clinical stage. Our J.POD cGMP biomanufacturing facilities are designed to deliver biologics drug substance for first-in-human clinical trials all the way through to commercial production.
Early-Phase Clinical Supply
We manufacture antibody and antibody-related biotherapeutics for first-in-human and early-phase clinical trials in our continuous manufacturing platform. Early-phase clinical trials are typically supplied from our hybrid continuous platform and a 500 L bioreactor. These runs can be executed from our J.PLANT facility in Seattle or one of our J.POD manufacturing sites.
Using continuous manufacturing for supplying early-phase clinical trials can offer significant benefits over fed-batch production by reducing the need for resupply runs. These benefits include:
- Cost-savings through avoiding buying extra batches
- Consistency of material used between different clinical trials
- Time-savings by avoiding scheduling conflicts in manufacturing operations
Performing early-phase clinical manufacturing with a continuous bioprocess allows partners to avoid switching from fed-batch to continuous production during their clinical journey and allows them to take advantage of lower cost of goods, greater agility, and lower risk during late-phase development.
Using continuous manufacturing for supplying early-phase clinical trials can offer significant benefits over fed-batch production by reducing the need for resupply runs. These benefits include:
- Cost-savings through avoiding buying extra batches
- Consistency of material used between different clinical trials
- Time-savings by avoiding scheduling conflicts in manufacturing operations
Performing early-phase clinical manufacturing with a continuous bioprocess allows partners to avoid switching from fed-batch to continuous production during their clinical journey and allows them to take advantage of lower cost of goods, greater agility, and lower risk during late-phase development.
Learn More in Our Recent Blog
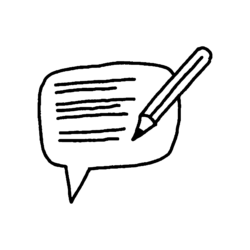
Late-Phase Clinical & Ph III Supply
We can support late-phase clinical programs, regardless of whether or not an intensified process has been developed beforehand. Our Commercial Process Development Services can leverage existing cell lines and support the switch from fed-batch to perfusion cultures and fully continuous modes ready for late-phase clinical and commercial manufacturing.
By manufacturing biopharmaceuticals for late-phase clinical supply in our continuous manufacturing platform you can mitigate scale-up risks while reaping the benefits of lower COGS and a more adaptable supply chain in preparation for commercialization.
Commercial Supply for Marketed Products
We have a fully end-to-end continuous biomanufacturing platform for the commercial supply of marketed biopharmaceutical products. This commercial manufacturing platform features one or two cell culture bioreactors operated in perfusion mode. Our J.POD facilities in Redmond, USA and Toulouse, France (EU) are ideal for the commercial supply of marketed biologics and are capable of delivering over 2,000 kg of antibody per year.
Benefits of a Continuous Process for Commercial Supply
Increased Biomanufacturing Agility
- Individualized batch outputs from 5 to over 2,000 kg to meet fluctuations in market demand
- <2 years for a new facility with our J.POD design
- Flexible manufacturing expansion using off-site constructed POD modules
Lower Bioproduction Risk
- Tunable product quality allows process optimization without regulatory risk
- Avoid geopolitical instability with cloned J.POD facilities in US & EU
- Option to integrate continuous manufacturing platform into partners’ facility
Lower Antibody Manufacturing Costs
- 75% reduction in COGM targeting <$50/g
- Two thirds reduction in CAPEX compared to other commercial-ready facilities
- Small footprint facilities with lower operating costs